Die Lean-Methode stammt aus Japan (Toyota Production System) und ist DIE Standard-Optimierungsmethode für Produktionssysteme. Es existiert eine unzählige Anzahl von Büchern und Artikel über dieses Thema, da dieser Verbesserungsansatz universell einsetzbar ist in vielen Bereichen (Lean Thinking, Lean Healthcare, Lean Administration, usw.).
Das Ziel dieses Artikels ist also nur das Aufzeigen der wichtigsten Elemente dieser für die Produktionssteuerung angewendeten Methode.
Grundidee
Die Grundidee der Lean-Methode ist sehr einfach, da sich eigentlich alle Konzepte und Werkzeuge nur um die Frage drehen, wie Aktivitäten ohne Wertschöpfung für den Kunden vermieden werden können. Gemäss der Lean-Methode gibt es sieben solche Aktivitäten oder Verschwendungen (= muda auf Japanisch):
- Überproduktion: Die Überproduktion entspricht der Produktion, für welche es keinen Kundenbedarf gibt. Dies ist die kritischste Verschwendung, da sie alle Produktionsprozesse betrifft. Oft sind sie ein Zeichen von einer schlechten Prozessbeherrschung (Fehler) oder von zu langen Durchlaufzeiten (zu hohe Lager- und Umlaufbestände);
- (Zu hohe) Lagerbestände: Eine weitere wichtige Verschwendung sind hohe Lager- und Umlaufbestände, da Sie Kapital binden und zu hohen Durchlaufzeiten führen;
- Transporte: Transporte entsprechen den Bewegungen der Produkte zwischen entfernten Lieferanten und Produktionsstandorten;
- Bewegungen: Unnötige Bewegungen zwischen Arbeitsprozessen können oft ergonomische Probleme verursachen;
- Wartezeiten: Wartezeiten werden oft durch Warteschlangen vor Prozessen verursacht. Oft sind solche Wartezeiten ein Zeichen einer mangelnden Synchronisation zwischen den verschiedenen Produktionsprozessen;
- Fehler: Fehler entsprechen allen Aktivitäten und Produkten, welche nicht den Spezifikationen oder Normen entsprechen;
- (Zu) komplizierte Prozesse: Zu komplizierte Prozesse sind schwierig zu beherrschen und erfordern einen (zu) grossen Steueraufwand. Solche Prozesse erzeugen oft auch eine Überqualität, welche die Produktpreise unnötig erhöht.
Die geniale Idee der Lean-Methode ist, dass die Leistung erhöht wird durch die Reduktion der Verschwendungen und nicht durch das Erhöhen der Kapazitäten. Das Ziel einer Produktion ohne Verschwendungen kann erzielt werden durch Produktionsinseln und den One-Piece-Flow (minimale Losgrössen und minimale Transportwege), welche eine perfekt synchronisierte Produktion erlauben.
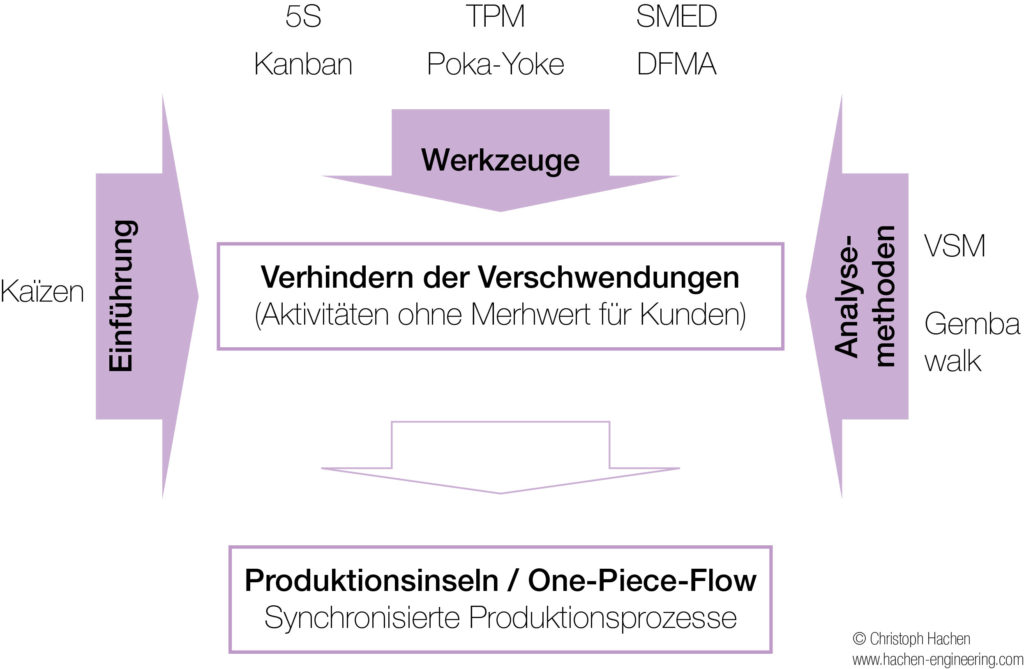
Werkzeuge
Die Lean-Werkzeuge erlauben das Reduzieren der Verschwendungen in den verschiedenen Aktivitäten des Produktionsprozesses (Wartung, Rüsten, Steuern des Materialflusses, usw.).
5S
Die 5S-Methode ist das fundamentale Lean-Werkzeug und ist abgeleitet von den fünf japanischen Verben Seiri (= Das Nützliche vom Unnützlichen trennen), Seiton (= Ordnen), Seiso (= Säubern), Seiketsu (= Standardisieren) und Shitsuku (= Disziplin und Verbessern). Die 5S-Methode wird oft am Anfang eines Lean-Projektes eingeführt, da ein sauberes, sicheres und geordnetes Arbeitsumfeld für alle Lean-Konzepte unabdingbar sind.
TPM
TPM (= Total Productive Maintenance) ist ein Lean-Werkzeug, welches die Produktivität der Produktionsmittel durch eine standardisierte Instandhaltung optimiert. Die Grundideen dieser Methode sind 1) die Anwendung der 5S-Methode (Produktionsmittel in einem tadellosen Zustand), 2) die Visualisierung des Maschinenzustandes für ein schnelles und einfaches Erkennen von Störungen, 3) das Einbinden aller Mitarbeiter in Instandhaltungsaktivitäten und 4) das Messen und Verfolgen der Gesamtanlageneffektivität (= OEE = Overall Equipment Effectiveness).
SMED
SMED (= Single Minute Exchange of Dies) ist ein Lean-Werkzeug für die Reduktion der Rüstzeiten. Diese Methode basiert auf der Tatsache, dass Rüstaktivitäten schon vor dem Stopp der Maschine durchgeführt werden können.
Kanban
Die Kanban-Methode (Kanban = Karte auf Japanisch) erlaubt die Regulierung des Materialflusses basierend auf dem Ziehprinzip (verbrauchsorientierter Materialfluss). Diese Methode verhindert die Überproduktion und verbessert die Synchronisation zwischen dem Lieferanten und den Kunden.
Poka-Yoke
Poka-Yoke ist das Lean-Werkzeug für das schnelle und automatische Erkennen von Fehlern in der Produktion. Solche Fehler sollten so rasch wie möglich erkannt und verhindert werden, da sie zu hohen Ausschussraten und zu Unterbrüchen des gesamten Materialflusses führen. Die Poka-Yoke-Methode kann mit einfachen (zum Beispiel mechanische Einrichtungen, welche ein falsches Montieren verhindern) oder mit komplexeren (elektronische Sensoren) Mitteln eingeführt werden.
DFMA
Die DFMEA-Methode (= Design for Manufacturing and Assembly) ist oft der Schlüssel für das Erreichen von signifikanten Verbesserungen der Produktivität. Diese Methode verbessert das Design der Produkte, damit einfachere und schnellere Produktionsprozesse eingeführt werden können. Typische DFMA-Lösungen sind die Standardisierung der Komponenten und Baugruppen (Modularisierung), das Einbinden von Poka-Yoke-Prinzipien (Verhindern von Montagefehler) sowie die Reduktion der Anzahl der Komponenten und der Stücklistentiefe.
Analysemethoden
Die folgenden Lean-Analysemethoden sollten vor dem Einsatz der verschiedenen Lean-Werkzeuge angewendet werden, um eine zielgerichtete Einführung der Lean-Methode zu garantieren.
VSM (Wertstromanalyse)
Die Wertstromanalyse (= VSM = Value Stream Mapping) ist ein visuelles Werkzeug für die Analyse und Darstellung des gesamten Material- und Informationsflusses und den Verschwendungen (Wartezeiten, Transporte, Aktivitäten mit/ohne Wertschöpfung, usw.). Wertstromanalysen werden oft bei der Einführung der Lean-Methode verwendet für die Definition eines ersten Aktionsplans.
Gemba walk
Die Gemba-Walk-Methode entspricht der Analyse «vor Ort», da effiziente Lösungen oft nur gefunden werden können, wenn die wirklichen Probleme auf Prozessebene auch erkannt wurden. Gemba-Walk-Analysen werden mit allen betroffenen Mitarbeitern durchgeführt und unterstützen den kontinuierlichen Verbesserungsprozess durch regelmässige Audits aller kritischen Prozesse.
Einführung der Lean-Methode
Trotz der Einfachheit seiner Konzepte ist die Einführung der Lean-Methode sicher kein müheloses Unterfangen. Viele Unternehmensprozesse müssen neu überdenkt werden und das Veränderungsmanagement wird ein wichtiger Erfolgsfaktor. Aus diesem Grunde wird die Lean-Methode oft innerhalb eines kontinuierlichen Verbesserungsprozesses eingeführt, um nachhaltigere Ergebnisse erzielen zu können.
Kaizen
Ein Kaizen (= kontinuierliche Verbesserung auf Japanisch) ist eine Verbesserungsaktion, bei welcher Lean-Lösungen kollektiv eingeführt werden basierend auf dem «gesunden Menschenverstand». Die gefundenen Lösungen sollten einfach zu implementieren sein und keine grossen Investitionen verursachen. Eine Kaizen-Verbesserungsaktion dauert meistens zwischen drei und fünf Tagen und beinhaltet die folgenden Etappen:
- Bildung der Arbeitsgruppe: Die Arbeitsgruppe sollte aus 5 bis 8 Mitarbeitern bestehen, welche mindestens alle betroffenen Funktionen abdecken (Produktion, Qualität, Planung, Finanz/Controlling, usw.). Die Arbeitsgruppe sollte ein bis zwei Wochen vor der eigentlichen Kaizen-Aktion gebildet werden;
- Analyse der aktuellen Situation (Tag 1): Analyse der vorhandenen Leistungskennzahlen, Ausführen einer Wertstromanalyse und/oder eines 5S-Audits sowie Beobachtungen «vor Ort»;
- Suche von Lösungen (Tag 1): Suche von mindestens 2 bis 6 Lösungsvorschlägen;
- Auswahl der Lösungen (Tag 2): Auswahl der Lösungen in Bezug auf ihre Machbarkeit und Effizienz;
- Kontrolle der Lösungen (Tag 2): Kritische Analyse der gewählten Lösungen mit Hilfe von Simulationen sowie Schätzung des Verbesserungspotentials;
- Einführung der Lösungen (Tag 3 und 4): Einführung der gewählten Lösungen;
- Einführung der Lösungen (Tag 3 und 4): Einführung der gewählten Lösungen;
- Auswerten der Lösungen (Tag 3 und 4): Auswertung der durch die eingeführten Lösungen verursachten Verbesserungen;
- Abschluss (Tag 4): Präsentation der Lösung an alle betroffenen Mitarbeiter sowie Erstellen eines Aktionsplans für die Behandlung der noch offenen Punkte.
Zusammenfassung
Die Lean-Methode ist DIE Standard-Optimierungsmethode für industrielle Organisationen. Durch das Anwenden der Basis-Werkzeuge wie 5S oder TPM können mit Hilfe dieser Methode relativ leicht (lokale) Verbesserungen der Produktionsumgebung erzielt werden. Signifikative Leistungsverbesserungen der gesamten Logistikkette können jedoch nur erreicht werden, wenn die ganze Organisation in einen (oft langen und beschwerlichen) kontinuierlichen Verbesserungsprozess eingebunden werden kann.
Referenzen
- George M. L., J. Maxey, D. Rowlands und M. Price. 2004. The Lean Six Sigma Toolbook: A Quick Reference Guide to 100 Tools for Improving Quality and Speed. McGraw-Hill, New York (in Englisch)
- Liker, J. K. 2020. The Toyota Way: 14 Management Principles from the World’s Greatest Manufacturer. McGraw-Hill, New York (in Englisch)
- Robinson A. 1990. Modern Approaches to Manufacturing Improvement – The Shingo System. Productivity Press, Portland (in Englisch)
- Takeda H. 2006. The synchronized production system. Kogan Page, London (in Englisch)