Die Beherrschung der Komplexität ist eines der wichtigsten Themen in der Produktionsplanung und -steuerung, sowie des in französischer Sprache erschienen Buches Gestion des Opérations – Une approche pragmatique. Jeder Planer von Logistikketten ist konfrontiert mit der Wahl und Optimierung einer grossen Anzahl von Planungsparameter, welche konstant an die geänderten Randbedingungen angepasst werden müssen. Um diese Planungskomplexität besser beherrschen zu können, ohne dabei kompliziert zu werden, schlägt der pragmatische Ansatz die folgende Vorgehensweise vor:
Optimale Anwendungsgebiete: Das falsche Anwenden von Planungsmethoden ausserhalb des idealen Anwendungsgebietes kann eine der wichtigsten Gründe für die Erhöhung der Planungskomplexität sein. Im pragmatischen Ansatz werden vor allem hybride Lösungen vorgeschlagen, in welchen die Planungsmethoden gemäss dem optimalen Anwendungsgebiet kombiniert werden;
Fundamentale Materialflussgesetze: Durch das Anwenden von Regeln, welche von den Materialflussgesetzen abgeleitet worden sind (zum Beispiel Limitierung des Umlaufbestandes), kann die Komplexität massgeblich reduziert werden und gleichzeitig die Leistungsfähigkeit verbessert werden;
Vereinfachungsstrategien: Die Anwendung von Vereinfachungsstrategien vereinfacht die Planung und erhöht dabei die Planungssicherheit. Dadurch kann auf den Einsatz von komplexen Optimierungsmethoden verzichtet werden (zum Beispiel Advanced Planning ans scheduling APS), welche oft einen sehr hohen Implementierungsaufwand verursachen.
Motivation
Die Aufgabe der Planung wurde, wie treffend im Buch von Carol Ptak und Chad Smith über das DDMRP (Demand Driven MRP) erklärt, über die letzten Jahrzehnte wegen den folgenden Entwicklungen immer schwieriger:
- Entwicklung von lokalen Logistikketten zu internationalen Netzwerken von Unternehmen;
- Immer kürzere Produktelebenszyklen;
- Die Kunden verlangen immer kürzere Lieferzeiten;
- Immer komplexere Produkte mit integrierter Mikroelektronik;
- Ein erhöhter Druck zur Reduktion der Bestände;
- Immer weniger sichere Vorhersagen;
- Etc.
Ptak und Smith nennen diese Situation «The New Normal». Dies heisst, dass die Planung und Steuerung von aktuellen Produktionssystemen immer schwieriger mit klassischen (analytischen) Werkzeugen wie MRP zu realisieren ist. Auch die Lean-Methode, welche schlanke und einfach zu steuernde Materialflüsse zum Ziel hat, ist leider nicht in allen «Produktionsumgebungen» einfach zu implementieren. Dies betrifft vor allem die Kanban-Methode, welche hauptsächlich für Produkte mit regelmässigem Bedarf angewendet werden kann.
Die grosse Anzahl von verfügbaren Konzepten für die Produktionssteuerung (Lean, MRP, DDMRP, POLCA, Demand Flow Technology, Advanced planning and scheduling APS, Theory of Constraints, usw.) reflektiert die Schwierigkeit der Aufgabe und zeigt auf, dass die alleinige Wunderlösung nicht existiert.
Die Systemtheorie gibt noch einen weiteren interessanten Einblick in die Frage der Kontrolle und Steuerung von komplexen Systemen.
Systemtheorie
Die Systemtheorie gibt eine Antwort auf die Frage, wie und unter welchen Voraussetzungen komplexe System kontrolliert und gesteuert werden können. Im Buch von Gerald M. Weinberg über dieses Thema wird der Anwendungsbereich von mathematischen Modellen in Bezug auf die Komplexität und den Zufallsgrad aufgezeigt. Wie auf dem nächsten Bild gezeigt können die drei Bereiche I (einfache Systeme à analytische Lösungen), II (komplexe unorganisierte Systeme à statistische Lösungen) und III (komplexe organisierte Systeme) definiert werden.
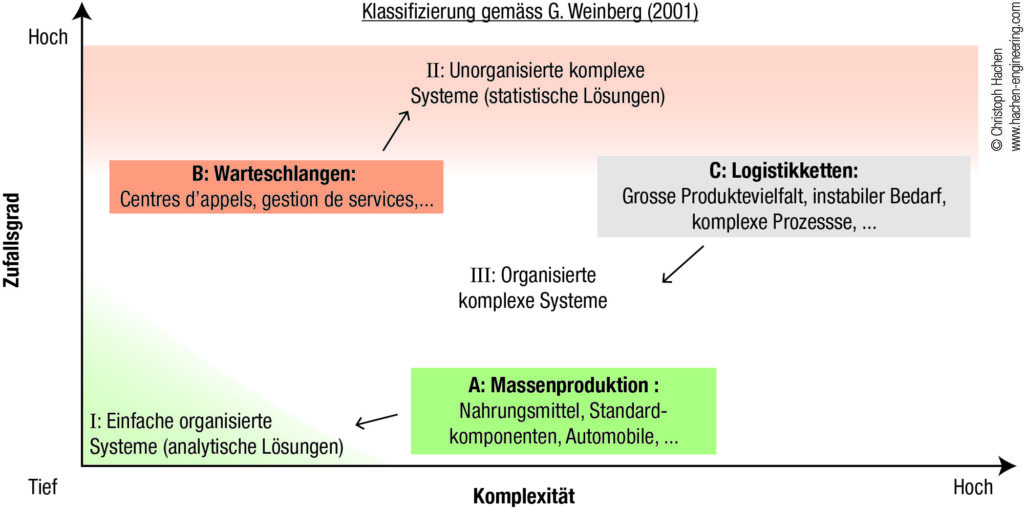
Im Gegensatz zu komplexen unorganisierten und einfachen Systemen gibt es also für komplexe organisierte Systeme keine mathematischen Lösungen. Das nichtlineare Verhalten von offenen Systemen wie Logistikketten verhindert den Einsatz von präzisen analytischen Werkzeugen.
Das Gesetz der erforderlichen Varietät von Ashby (law of requisite variety) bestätigt diese Tatsache. Nach diesem Gesetz kann ein System nur kontrolliert werden, wenn das Kontrollsystem über mindestens die gleiche Varietät besitzt. Die Varietät eines Systems ist die Anzahl der möglichen Zustände aller seiner Parameter und Eigenschaften.
Das Gesetz des abnehmenden Ertrags (law of diminishing returns) zeigt ebenfalls die Schwierigkeiten auf, welche bei der Optimierung von (komplexen) Systemen auftreten können. Laut diesem Gesetz wird das Verhältnis zwischen Ertrag und Aufwand mit zunehmendem Optimierungsaufwand für ein gegebenes System immer kleiner. Ab einem gewissen Grad können Optimierung sogar kontraproduktiv sein, wenn der Ertrag vernachlässigbar oder sogar negativ ist.
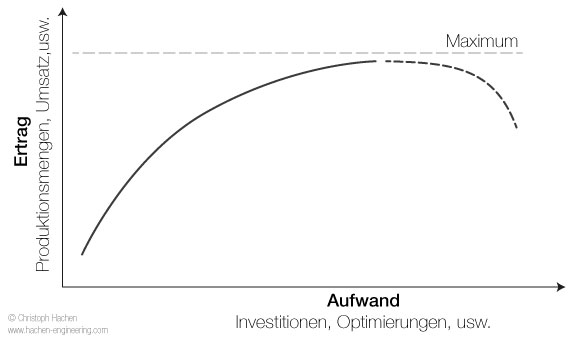
Die Systemtheorie bestätigt also die Schwierigkeit, mit Hilfe von mathematischen Modellen verlässliche und präzise Lösungen für die Produktionsplanung zu erhalten. Zudem können Bestrebungen nach optimalen Resultaten sehr hohe Investitionen in Zeit und Geld nach sich ziehen, welche den erzielten Ertrag oft nicht rechtfertigen.
Der pragmatische Ansatz
Für die Produktionsplanung und -steuerung von komplexen Logistikketten zielt der pragmatische Ansatz also darauf ab, eher «robuste» Lösungen mit begrenztem Aufwand zu finden als «optimale» Lösungen mit grossem Aufwand zu suchen.
Optimale Anwendungsgebiete
DIE Wunderlösung für die Produktionssteuerung existiert also leider nicht. Allerdings haben viele Konzepte einen spezifischen Anwendungsbereich, in welchem sie sehr gute Ergebnisse liefern. Ein typisches Beispiel ist die Kanban-Methode, welche sehr interessante Eigenschaften besitzt wie die Begrenzung der Umlaufbestände sowie das Verhindern der Überproduktion. Eine generelle Anwendung dieser Methode wäre aber eher kontraproduktiv, da sie gute Ergebnisse nur in Produktionsumgebungen mit stabilen Bedarfsmengen und Prozessen liefert.
Der pragmatische Ansatz bevorzugt also gemischte oder hybride Lösungen, bei welchen verschiedene Konzepte entsprechend ihrem Anwendungsgebiet kombiniert werden, um eine stabilere Leistung des Gesamtsystems zu erhalten. Das typische Beispiel ist das Kombinieren der Kanban-Methode (Standardprodukte), der MRP-Methode (Auftragsfertigung) sowie der Serienfertigung (Schlüsselprodukte) für die Produktionssteuerung. Das wichtigste Werkzeug für die richtige Auswahl der optimalen Anwendungsgebiete der verschiedenen Optionen (Produktionssteuerung, Vorhersagen, Planungsparameter, Optimierungsmethoden, usw.) ist die ABC-XYZ-Analyse kombiniert mit dem Produktelebenszyklus.
Fundamentale Materialflussgesetze
Das Verhalten vom Materialfluss wird von Gesetzten beschrieben, welche den Zusammenhang von logistischen Grössen wie Durchlaufzeiten, Umlaufbestände und Leistung aufzeigen (Hopp und Spearman, Nyhuis und Wiendahl). Handlungen oder Entscheide, welche diese universell anwendbaren Gesetze ignorieren, führen also mit hoher Wahrscheinlichkeit zu einer schlechteren Gesamtleistung des Produktionssystems. Ein solches typisches Beispiel ist das Überlasten von Produktionseinheiten, um eine hohe Leistung zu gewährleisten. Diese (lokalen) Optimierungen garantieren effektiv eine höhere Leistung von gewissen Produktionseinheiten, das ganze Produktionssystem ist aber infolge der daraus resultierenden Negativ-Spirale von hohen Umlaufbeständen und Durchlaufzeiten viel schwieriger zu steuern und zu planen. Das Beherrschen und die Kontrolle der Umlaufbestände ist integraler Bestandteil des pragmatischen Ansatzes.
Vereinfachungsstrategien
Vereinfachungsstrategien sind ein unabdingbares Hilfsmittel für die Produktionsplanung und -steuerung. Anstelle die Planungsparameter für jeden einzelnen Artikel zu optimieren, können allgemeine Regeln definiert werden für Artikelgruppen, welche aufgrund einer Bedarfsklassifikation (ABC-XYZ-Klassifizierung und Produktelebenszyklus) definiert worden sind (siehe ABC-Konfiguration).
Ein anderer wichtiger Ansatz ist die hierarchische Planung, welche verglichen werden kann mit dem in der Informatik verwendeten Teile-und-herrsche-Verfahren (divide and conquer). Das Ziel bei beiden Methoden ist, ein ursprünglich komplexes Gesamtproblem in einfacher zu beherrschende Unterprobleme aufzuteilen. Die Planung wird also in eine Langfrist- (Zeiteinheit=Monat, Produktefamilien), Mittelfrist- (Zeiteinheit=Woche, Endprodukte) und Kurzfristplanung (Zeiteinheit=Tag, Produkte und Komponenten) aufgeteilt. Generell entspricht die Langfristplanung dem Sales and Operations Planning Process S&OP.
Das Pareto-Prinzip sowie die Engpasstheorie (theory of constraints) helfen ebenfalls dabei, im Zusammenspiel mit der hierarchischen Planung das Wichtige vom Unwichtigen zu trennen. Dabei geht es also vor allem darum, in einem ersten Schritt die Planung der kritischen Ressourcen (Engpassoperationen) sowie der wichtigsten Materialflüsse (Hauptprodukte) sicherzustellen.
Limitierte Ressourcen
Ein Vorteil des pragmatischen Ansatzes ist die Tatsache, dass Lösungen mit wenig Aufwand in Zeit und Geld gefunden werden können. Ein typisches Beispiel ist die visuelle Steuerung der Produktion. Lösungen wie MES (Manufacturing Execution System) können in ERP-Systeme integriert werden und erlauben das Verfolgen der Produktionsprozesse in Echtzeit. Die Erfahrung zeigt aber, dass diese interessanten Lösungen eine hohe Datenqualität benötigen, welche nicht immer einfach zu erreichen ist. Der pragmatische Ansatz bevorzugt also visuelle Planungstafeln, welche das einfache Planen und Steuern von Produktionsabteilungen erlauben zum Bruchteil der Investitionen für ein MES.
Zusammenfassung
Der pragmatische Ansatz für die Produktionsplanung hat zum Ziel, die Planungskomplexität mit möglichst einfachen Mitteln besser zu beherrschen. Der präsentierte Ansatz entspricht keiner Neuentwicklung, sondern eher einer ausgewogenen Mischung von Methoden und Konzepten, welche sich in der Praxis bewährt haben. Zudem wird auf das Anwenden von komplexen Optimierungsmethoden verzichtet, um den Aufwand in Zeit und Geld möglichst gering zu halten. Falls die Ressourcen jedoch «unbegrenzt» vorhanden sind, kann der pragmatischen Ansatz als Ausgangspunkt für weitergehende Optimierungen (Lean-Methode) angesehen werden. Die folgende Figur fasst die wichtigsten Aspekte der pragmatischen Planung zusammen
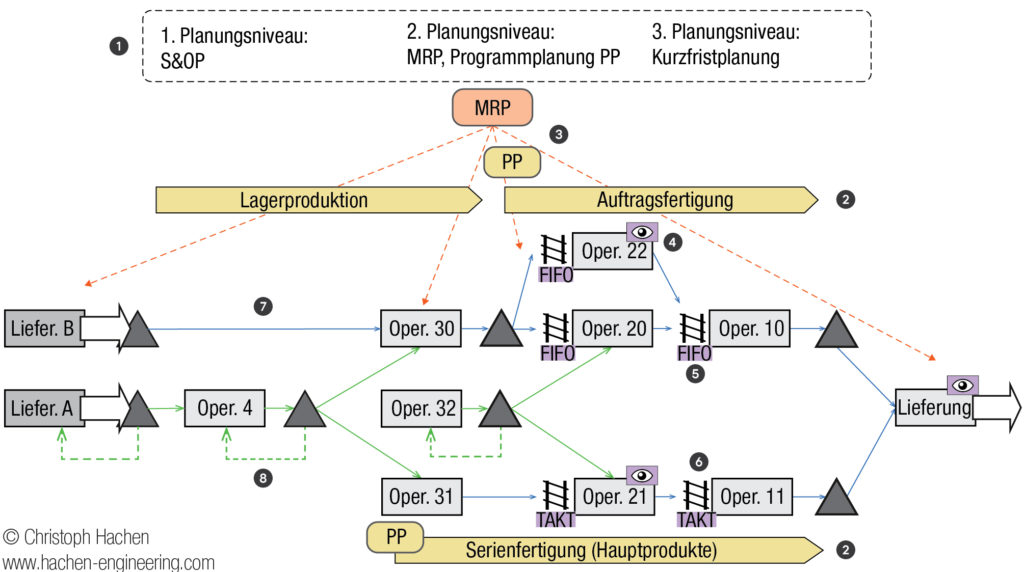
- HierarchischePlanung: Lang-, Mittel- und Kurzfristplanung;
- Produktionsstrategien: Serienfertigung (Hauptprodukte), Lager- und Auftragsfertigung;
- MRP: Auftragssteuerung und Programmplanung (PP);
- Visuelle Planung: Visuelle Planung der kritischen Ressourcen;
- Materialfluss: Limitierung des Umlaufbestandes und FIFO-Prioritätenregel;
- TAKT: Synchronisierter Materialfluss für Hauptprodukte und/oder standardisierte Endprodukte;
- Auftragsgesteuerter Materialfluss: Kundenspezifische Produkte
- Verbrauchsgesteuerter Materialfluss: Standardisierte Komponenten und Halbfabrikate.
Références
- Ptak C. und C. Smith. 2019. Demand Driven Material Requirements Planning (DDMPR), Version 3. Industrial Press, Inc. (in Englisch)
- Weinberg, G. 2001. An introduction to General Systems Thinking. Weinberg & Weinberg (in Englisch)
- Hopp W.J. und M.L. Spearman. 2000. Factory Physics : Foundations of manufacturing management, 2end edition. McGraw-Hill, New York (in Englisch)
- Nyhuis, P. et H.-P. Wiendahl. 1999. Logistische Kennlinien. Springer-Verlag, Berlin Heidelberg