Ein Vorteil von modernen ERP-Systemen ist die Tatsache, dass es grundsätzlich keine Grenze gibt bei der Anzahl und Komplexität der verwaltenden Produkte. In einem Markt mit immer komplexeren Produkten mit immer kürzeren Produktelebenszyklen ist es keine Ausnahme, dass mehr als 10’000 Artikel (Endprodukte, Baugruppen, Komponenten, Rohmaterial, usw.) in einem Unternehmen verwaltet werden müssen. Bei einer Annahme von mindestens drei bis fünf Planungsparameter pro Artikel kommt man daher schnell auf eine Anzahl von über 50’000 Planungsparameter, welche verwaltet und optimiert werden müssen. Je nach Stabilität der Produktionsumgebung und der verfügbaren Ressourcen kann dies einer sehr schwierigen Aufgabe entsprechen.
Die Grundidee der ABC-Konfiguration ist die Definition von Planungsregeln basierend auf einer kombinierten ABC-Analyse, welche dann auf die einzelnen Artikel angewendet werden können.
Konzept
Das Konzept der ABC-Konfiguration basiert auf der kombinierten ABC-Analyse, welche die Klassifizierung der Artikel in Bezug auf mehrere Kriterien erlaubt. Typische Kriterien sind das Volumen und die Stabilität der Nachfrage, der Produktelebenszyklus und die Produkteklassen. Je nach Produktionsumgebungen können aber noch andere Kriterien wir die Haltbarkeit (Lebensmittel) oder der Transportweg (Transportlogistik) hinzugefügt werden. In diesem Zusammenhang sollte darauf hingewiesen werden, dass die kombinierte ABC-Analyse aus messbaren und qualitativen Messgrössen bestehen kann.
Auf der Basis der kombinierten ABC-Analyse eines jeden Artikels können nun Regeln definiert werden für die Planungsparameter Losgrösse, Sicherheitslager und Materialflusskonzept. Die dadurch erhaltenen Werte entsprechen nicht unbedingt einem optimalen Wert, sondern eher einer korrekten Grössenordnung.
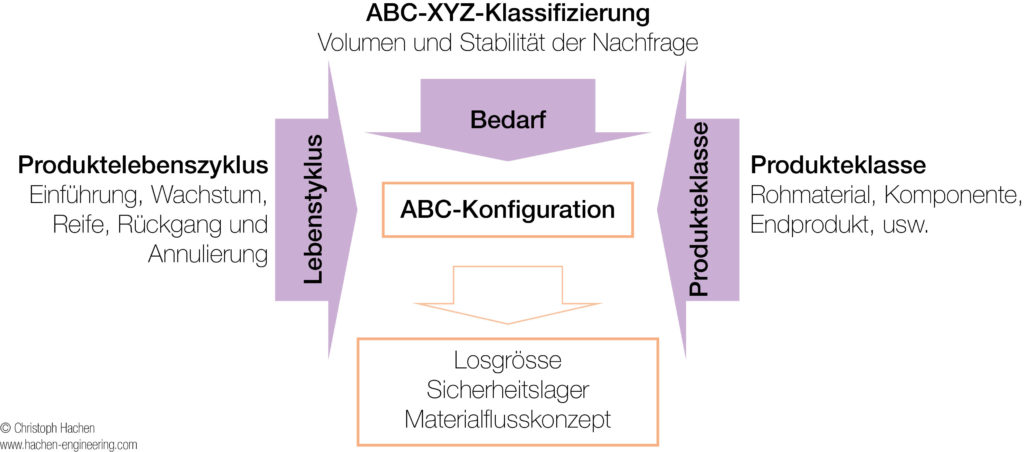
ABC-XYZ-Klassifizierung
Die ABC-XYZ-Klassifizierung ist die ideale Methode für das Messen des Volumens und der Regelmässigkeit (Stabilität) der Nachfrage zu messen. Sie basiert auf der ABC-Klassifizierung (Pareto) sowie der Messung der Variabilität der Nachfrage mit Hilfe des Variationskoeffizienten VarK (= Standartabweichung/Mittelwert). Für die Klassifizierung des Nachfragevolumens mit Hilfe der ABC-Analyse werden oft die Grenzwerte 80% (A-Klasse), 15% (B-Klasse) und 5% (C-Klasse) verwendet. Für die Klassifizierung der Nachfragevariabilität werden oft die Grenzwerte <0.8 (X-Klasse), 0.8 … 1.2 (Y-Klasse) und >1.2 (Z-Klasse) verwendet. Oft wird die ABC-XYZ-Klassifizierung basierend auf der Nachfrage der letzten 6 bis 12 Monate durchgeführt.
Mit Hilfe der ABC-XYZ-Klassifizierung können nun empirische Regeln definiert werden für die Planungsparameter Losgrösse, Sicherheitslager und Materialflusskonzept. Die Parameter Losgrösse und Sicherheitslager werden berechnet auf der Basis der mittleren Nachfrage während die Wiederbeschaffungszeit NMW. Unter idealen Bedingungen (stabile Nachfrage und Wiederbeschaffungszeiten) entspricht also die Losgrösse exakt dem Wert von NMW. Mit Hilfe der folgenden Formeln können nun die Losgrössen und die Sicherheitslager definiert werden:
Losgrösse = fvar x NMW
Sicherheitslager = fsec x NMW
mit (mittleres Level):
XYZ-Klasse | X | Y | Z |
---|---|---|---|
fvar (mittel) | 1.5 | 3 | 6 |
ABC-Klasse | A | B | C |
---|---|---|---|
fsec (mittel) | 1.0 | 0.5 | 0.2 |
Die Lieferfähigkeit von A-Artikel (Schlüsselprodukte) wird also sichergestellt durch erhöhte Sicherheitslager, während Nachfragespitzen von Z-Artikel durch erhöhte Losgrössen abgefangen werden. Die empirischen Werte der Faktoren fvar und fsec entsprechen einer Schätzung, welche je nach Produktionsumfeld oder Produkteklasse variieren kann.
In Bezug auf die Auswahl der Materialflusskonzeptes wird der gezogene Materialfluss (Kanban-Methode) und die Serienfertigung für X-Artikel mit stabiler Nachfrage empfohlen.
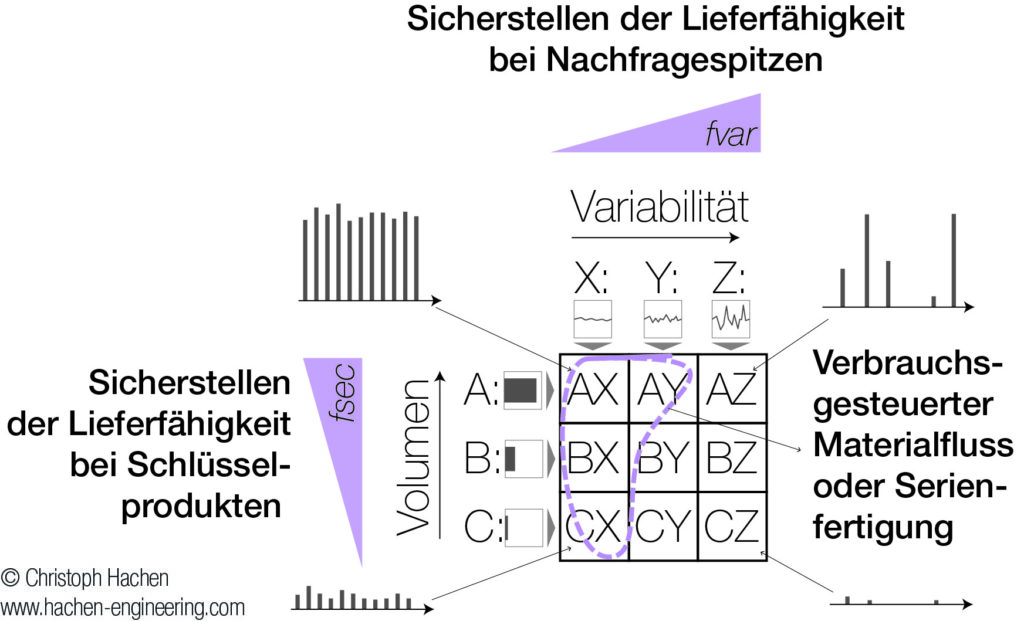
Produktelebenszyklus
Der Produktelebenszyklus hat einen signifikanten Einfluss auf die Auswahl der Planungsparameter vor allem am Anfang sowie am Ende des Lebenszyklus. Am Anfang des Produktelebenszyklus ist es oft wichtig, eine hohe Verfügbarkeit des Artikels bei seiner Einführung sicherzustellen (Einführungskampagne). So werden für diese Phase oft die Lagerfertigung und Sicherheitslager definiert. Am Ende des Produktelebenszyklus ist es oft wichtig, dass Risiko der Obsoleszenz zu reduzieren. In dieser Phase sind also die Auftragsfertigung sowie die Aufhebung aller Sicherheitslager die typische Wahl. Während des Reife-Produktionslebenszyklus können die Planungsparameter gemäss der ABC-XYZ-Klassifizierung definiert werden.
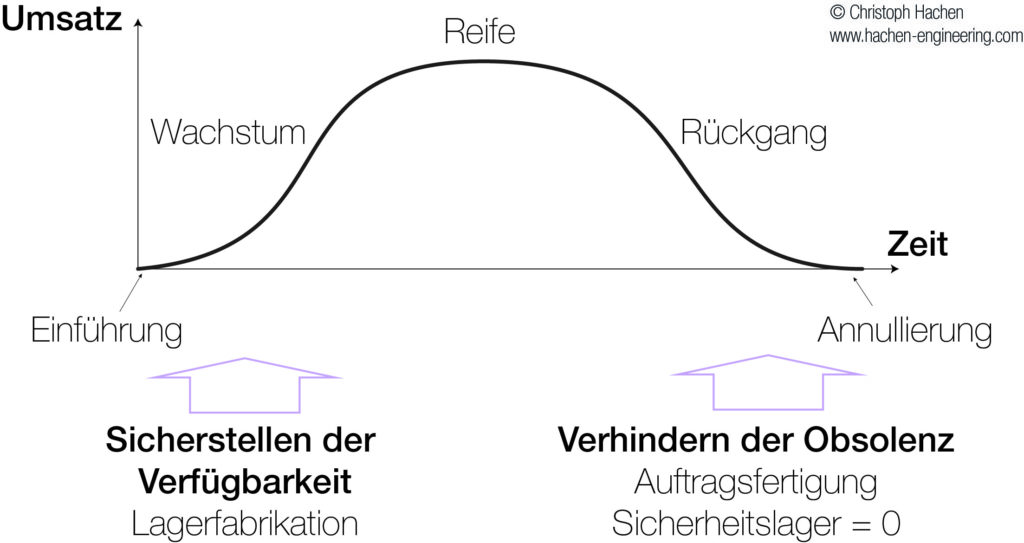
Produkteklasse
Die Auswahl des Standortes der Sicherheitslager in der Logistikkette hängt ab von Faktoren wie der gewählten Produktionsstrategie, der Wichtigkeit der Komponenten sowie der Zuverlässigkeit der Produktionsprozesse. Generell ist es aber eher wünschenswert, Sicherheitslager am Anfang der Logistikkette zu haben als an ihrem Ende. Ein Lieferengpass bei einem Rohmaterial oder eines Grundkomponenten kann die ganze Lieferkette stoppen, während ein Lieferengpass bei Baugruppen eher nur zu punktuellen Lieferengpässen bei Fertigprodukten führt.
Aus diesem Grunde können für Rohmaterial und Grundkomponenten höhere Werte der Parameter fvar und fsec gewählt werden als Fertigprodukte. Die folgenden Tabellen zeigen mögliche Levels bei der Auswahl der Parameter fvar und fsec (Level tief und hoch):
XYZ-Klasse | X | Y | Z |
---|---|---|---|
fvar (tief) | 1.2 | 2 | 4 |
ABC-Klasse | A | B | C |
---|---|---|---|
fsec (tief) | 0.5 | 0.2 | 0.0 |
XYZ-Klasse | X | Y | Z |
---|---|---|---|
fvar (hoch) | 2 | 4 | 8 |
ABC-Klasse | A | B | C |
---|---|---|---|
fsec (hoch) | 1.5 | 1.0 | 0.5 |
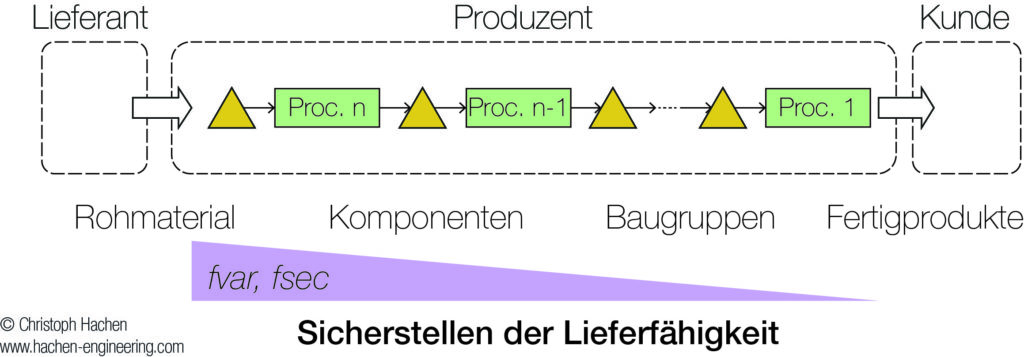
Anwendung
Die folgende Tabelle zeigt eine typische Auswahl der Planungsparameter basierend auf dem Produktelebenszyklus und der Produkteklasse:
Klasse | Lebenszyklus: Wachstum | Lebenszyklus: Reife | Lebenszyklus: Rückgang |
---|---|---|---|
Rohmaterial | Lagerfabrikation gemäss Einführungskampagne | ABCXYZ-Klasse, fvar und fsec hoch | Auftragsfertigung, Sicherheitslager = 0 |
Baugruppen | ABCXYZ-Klasse, fvar und fsec mittel | ||
Fertigprodukte | ABCXYZ-Klasse, fvar und fsec tief |
Basierend auf diesen optimalen Parameter können nun die Planungsparameter kontrolliert werden durch das Berechnen des Verhältnisses zwischen den aktuellen und optimalen Werten. Dabei können die kritischsten Artikel identifiziert werden, für welche die Lagerreichweite zu tief oder zu hoch ist.
Zusammenfassung
Die ABC-Konfiguration ist ein Entscheidungshilfe-Werkzeug, welches das Kontrollieren einer grossen Anzahl von Planungsparameter erlaubt. Es erlaubt das schnelle Aussortieren von kritischen Artikeln, für welche die Lagerreichweite zu tief oder zu hoch ist infolge von unzureichenden Losgrössen und Sicherheitslager. Die Auswahl der für die Kanban-Methode (oder Serienfertigung) geeigneten Artikel kann ebenfalls mit Hilfe der ABC-Konfiguration durchgeführt werden.